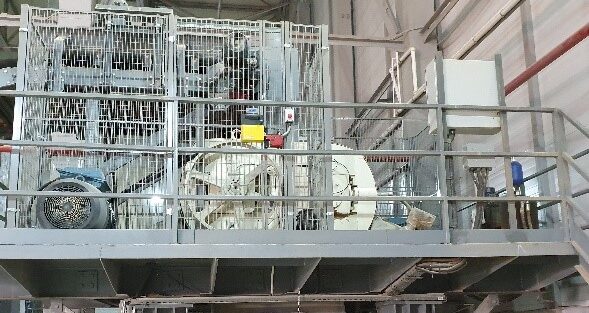
16 Jul Verdés new plant in Uzbekistan, Ceramitech Group
The new plant of the leading private conglomerates in Uzbekistan, Ceramitech Group, has a planned capacity of 1 200 t/day with a wide product portfolio from the local common bricks to large-size hollow blocks.
This challenged project started on October 2017. Together with SABO (who was the main contractor) and after several technical meetings, we agreed with them and the final customer the specifications as well as customization of the project and 20 months later the brick factory launched its activity.
The grinding as well as the shaping line was fully engineered by Verdés supported by the intensive trials made previously in the technological ceramic laboratory available on Verdés facilities. These tests guaranteed the best performance of granulometry as well as stiffness of the final products.
The grinding line starts with a robust primary crusher responsible of shredding big lumps of clay which will be reduced up to 20 times their original dimension.
Following the primary crusher there is wet grinding process made up of a disintegrator, roller mill and mixer. At the exit of the mixer, the grinding line guarantees 90 t/h and the mixture is aging on box storage with a capacity of 7.500 m3. The line allows to automatically bypass the aging area as required.
An automatic and precise reclaimer links the grinding area with the shaping line. This reclaimer is digitally connected with the feeder which give full flexibility for maintenance operations without affection on the daily production capacity of the plant.
Before reaching the extruder, the mixture is ground at 0,7mm by two roller mills in line and mixed by a circular screen feeder from where the mixture goes out 100% blended and homogenized. Both roller mills have an electronic and automatic gap adjustment to ensure the output granulometry.
At the end of the shaping line, there is the extruder Magna 775 which guarantee a production from 60 to 100 t/h with three types of products: solid brick, hollow brick and block. The extruder is held on an elevation bedframe which adjust the high of the extrusion axis depending on the type of product.
Likewise, as Verdés follows the philosophy of high quality to guarantee the quality and performance of the installed plant, a complete set of original spare parts was supplied together with the line. Verdés not only wants to be a machinery supplier but a partner with a solution that is not limited to equipment, but also provides business continuity (spare parts) and an infinity of services available to our customers.
In addition, one of the latest services proposed by Talleres Felipe Verdés is the customized online access that allows the client to have access to all the technical documentation related to their equipment and to maintain direct contact in relation to all after-sales matters such as spare parts, technical queries,….
In parallel, this modern installation has also been equipped with a completed ceramic laboratory including the grinding and shaping Verdés machinery. Thanks to this laboratory, Ceramitech Gorup technician can trial the optimal blends to obtain the highest performance on the final product.
Another new reference and project developed giving continuity to Talleres Felipe Verdés’ reputation since 1908 designing and manufacturing machinery on wet, semiwet and dry grinding process and soft and hard extrusion.